数字化时代,需搭建精益阶梯
- 2021/5/27 7:53:41 作者: 来源:UPS应用
-
精益生产起源于日本丰田,在成本控制、提高效率及质量等方面创造了强大的竞争优势,也成为所有制造企业争相复制的管理模式,大量制造企业从中获得了无法估量的进步。
精益生产起源于日本丰田,在成本控制、提高效率及质量等方面创造了强大的竞争优势,也成为所有制造企业争相复制的管理模式,大量制造企业从中获得了无法估量的进步。
随着制造业不断升级,精益生产的必要性也愈发凸显:国务院参事汤敏教授就指出,未来中国制造业向小批量、定制化的柔性制造转型。同时在提质增效、追求更高价值的目标驱动下,企业也要更加积极拥抱精益生产。
作为全球能源管理和自动化领域的数字化转型专家,拥有200多家工厂的施耐德电气在2020年Gartner全球供应链榜单中排名第四、蝉联工业制造类榜首。这一成绩背后,精益管理同样功不可没。施耐德电气中国供应链爱迪生专家严巍和李春生表示,精益是数字化与智能化管理的基础。

精益是迈向数字化、智能化的基础
何为精益?
严巍指出:简单理解精益,指的是企业的一切都以满足客户需求为中心,通过不断减少或消除工业全过程中的各种浪费提升自身竞争力。而作为供应链转型的基石,整个价值链都需遵循精益的工作方式——包括制造、物流、业务运营、研发、工业化等等——才能将基础打实,从而加速转型进程。
精益意味着追求更高、更严格的标准;以最小的投入,取得最大的产出——相比传统的大批量生产,它更灵活,能够根据客户要求调整生产,尤其能满足小批量、多品种、短交期、高品质的需求,对中小企业十分适用。面对多变的市场,精益生产能够对客户的定制化需求快速反应,帮助企业提高核心竞争力。
在生产过程中,精益理念尽可能地压缩一切可避免的成本、制止过量生产、消除直接和间接浪费,特别是通过高标准、高要求,减少残次品,让企业增加效益。通过对整个流程精益化,节省运营过程中的时间、人力、物力,进而最大化实现供应链的合理、高效和灵活。
如何精益?
严巍将精益概括为:以客户为核心,围绕生产过程、运营系统及企业文化等各个方面的不断优化。
首先,生产过程精益化:以客户需求为中心、减少浪费的同时提升质量。精益的出发点是减少浪费,而生产出不合格产品不仅增加成本,还会引发客户抱怨。因此,企业要提高产品和服务的质量,就要通过精益来优化生产过程、减少浪费和不良率,而不是简单地压缩成本、牺牲质量。
施耐德电气供应链质量管理爱迪生专家李春生表示,“精益管理和质量管理,实则你中有我、我中有你。”一直以来,施耐德电气将精益管理工具和六西格玛方法论结合在一起,形成独特的“精益六西格玛”管理和改进方法:既改进生产过程和产品质量、降低浪费、减少不增值的行为,也针所有业务流程进行改进,同时与广大供应商伙伴一起提升产品质量和交付绩效,实现“双赢”和“共生”。
该方法广泛应用于施耐德电气的工厂管理和持续改进,仅在2020年,中国的10家备货型生产工厂就通过效率提升和质量改进实现了超过2千万元的成本节约。
在数字化转型的大背景下,这套管理方法也在不断“升级”,结合数字化手段与工具,实现更大范围、更深入的颠覆性改进。李春生介绍,在过程质量方面,施耐德电气非常注重防错—采用以“零缺陷”为目标的管理思路,寻找生产过程中的薄弱点,并采取一定的措施让错误“不可能”产生、“不可能”成为不良品流出。“在此思想指导下,利用深度学习的图像识别技术,通过产线上的智能相机捕捉错误,已经在多个工厂落地应用,既提升质量也提升效率。”
其次,运营系统精益化:以生产效率为中心,各部门之间敏捷协同、服务生产。高品质的产品和服务要求价值链上的每个环节都能敏捷、高效运转。因此,不仅生产要精益,组织里的所有部门都应“做减法”,提升效率,助力生产。
比如一些常见的情况:物料部门把一整天甚至一周的物料集中送到生产线上,致使生产空间被大量占用;原材料不齐套导致生产周期过长;管理机制问题造成部门间沟通配合不畅等等。为解决类似问题,以精益思想为指导,施耐德电气独创了一套SPS体系(SchneiderPerformanceSystem),来提升各个部门的运营效率。从流畅的产线设计开始,到物料供应、维修,班组长及时响应问题,让各部门抛弃自我中心、建立服务意识,通过紧密配合大幅提高整个供应链的运营效率。在这一方法论的持续引领下,施耐德电气中国工厂每年生产率提升超过10%。
最后,企业文化精益化:全员参与,精益求精。“精益”不仅要追求高效生产,更要力求完美、持续超越。想真正实现这一点,离不开组织中每个人的认同与投入。严巍对此总结道,“与其说是培养精益的工厂,不如说要培养精益的人。”
调查显示,工厂95%的问题都与“看不见、够不着、来不及”有关,即信息不透明(15%)、管理有效性差(32%)、决策不及时(48%)。这反映出了精益思想在管理方式和文化层面的普遍缺失。
在精益文化的熏陶下,每个人都能充分发挥主观能动性:一线员工发现问题之后,第一时间尝试当场解决;解决不了的问题立刻进入一个“自下而上反映问题、自上而下支持解决”的信息流。这就是施耐德电气即时管理体系SIM(ShortIntervalManagement),也被称为“趁热打铁管理法”,目的在于:车间能解决的问题,当天得到解决和改善;如果解决不了,一线工人的问题会在五天之内直达工厂总经理,把管理者“拉到现场看问题”。
精益是数字化的坚实基础
在严巍看来,没有精益的基础,就无法发挥智能制造的效益。只有先把现有的工作简化、标准化,再做自动化、数字化,才能事半功倍,水到渠成。“正如建造雄伟的高楼必须先打好坚实的地基,精益管理就是数字化工厂发挥效益的基石。”
练就了深厚的精益内功之后,就可以利用数字化工具持续优化,包括标准化、可视化。例如施耐德电气的数字化精益系统LDS(LeanDigitalSystem)、全流程数字化运营工具等等,逐步推动产品级、设备级、工厂级的互联互通,让各种生产、库存数据、设备、人员状态、能源情况透明可见,并在各部门、各层级之间打通信息,进一步提高管理效率、能源效率,循序渐进地向绿色智能制造迈进。
作为长期合作伙伴,川开电气自2019年起与施耐德电气合作打造川开电气数字工厂。将精益管理与数字化工具有机融合,利用数字化工具固化项目管理流程,实现对过程的实时掌握,使项目成本清晰可控。建设完成三条精益产线布局和厂内物流运送,通过融合生产管理数字化系统,实现生产排产自动化,生产过程和生产效率透明化,生产问题解决及时化,有效地减少了生产现场的物料及在制品堆积,消除了生产过程黑洞。
当前,中国正从制造业大国向智能制造强国迈进,摒弃高耗能、粗放型的生产方式,转向为精细化、智能化的生产方式。精益生产正是中国制造业不断夯实竞争力、迈向国际价值链高端的阶梯。施耐德电气希望以自身的经验与技术赋能国内制造企业,通过精益管理咨询和培训,把技术和经验不断分享给客户、合作伙伴、供应商,带动产业升级,实现智造强国愿景。
编辑:Harris
精益生产起源于日本丰田,在成本控制、提高效率及质量等方面创造了强大的竞争优势,也成为所有制造企业争相复制的管理模式,大量制造企业从中获得了无法估量的进步。
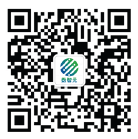