失效模式和影响分析(FMEA)的重点大多在过程FMEA上,但需要设计FMEA(DFMEA)来确保识别和预防潜在的与设计相关的失效。作者提供了执行成功的DFMEA所需的行动的简明回顾,以帮助读者理解这种分析的过程和目标。
失效模式和影响分析(FMEA)的重点主要集中在过程潜在失效模式和影响分析(PFMEA)上,但是需要设计潜在失效模式和影响分析(DFMEA)来确保识别和预防潜在的与设计相关的失效。
DFMEA格式的准确布局通常因行业和组织而异。DFMEA格式的措辞也可能不同,但内容通常是可比较的。例如,一个组织的DFMEA格式可能有一个“预防行动”字段,而不同的组织可能有一个用于相同用途的“当前的预防控制”字段。图1显示了用于电机活动盖板的通用构成DFMEA格式示例。
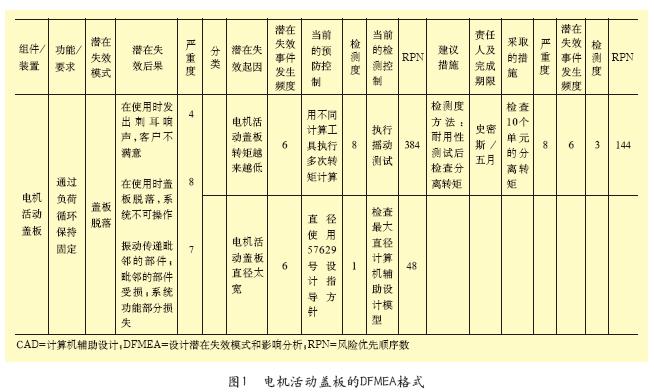
执行DFMEA
典型的DFMEA格式以一个用于评估元件或组件名称的字段开始。格式还可以包含用于描述其功能或需求的字段,或者用于描述其功能或需求两者之一的字段。功能是对元件或组件必须做什么的描述,一个组件可能有多个功能。例如,可能需要一个配件来确保密封性和抗腐蚀。识别元件或组件的功能是有帮助的,因为这些信息将提供对可能的失效模式的深刻理解,并对不符合功能要求现象的说明。可能的功能要求包括:
•提供安装点
•抗腐蚀
•提供可追溯性
•提供目前状况
•密封坚固性
•提供支持
另一种方法是列出元件或组件必须满足的要求。通常,这是技术规格,如“提供12伏”。要求必须是可测量的,因此,要求比功能提供更详细的信息。然而,这些信息在开发项目的早期可能是未知的,或者在项目的后期可能会发生更改。潜在要求包括:
•旋转范围14mm.
•七位数的可追溯编号
•洛氏硬度为70
•24小时抗盐雾腐蚀
•寿命达到10万次循环。
失效模式是指“产品或流程无法实现预期功能(设计意图或性能要求)的方式”[1]。例如,对于一个简单的螺栓盖板,一个可能的潜在失效模式是盖板松动。其他可能的潜在失效模式示例包括:
•卡住
•工作电压太高
•腐蚀
•部件松动
•不适合
•泄漏
重要的是要避免将失效模式与失效原因混淆,失效原因是失效模式发生的根本原因,或失效后果是失效模式发生造成的后果。如果失效原因、失效模式和失效后果之间存在混淆,请在白色书写板上列出澄清因果关系链中的步骤。例如,“压力舱壁厚过薄”可能导致裂缝,从而导致泄漏,导致整个系统失效。按照发生的顺序写下各个步骤,有助于弄清原因是什么,潜在失效模式是什么,以及潜在失效后果是什么。
一种潜在失效模式可能会导致多种潜在失效后果,或者一种失效后果会导致更多影响后果。例如,潜在失效模式“组件腐蚀”可能导致不同的后果,诸如“锈蚀穿过油漆层导致不可接受的难看外观”和“锈蚀导致系统失效的堵塞”。
或者,一种潜在失效模式只可能有一种直接后果,比如潜在失效起因“孔径公差过宽”,导致潜在失效模式“连杆过度自由摆动”,从而导致潜在失效后果“刺耳响声”。严重度等级应基于对最终系统造成的后果,因此理想情况下应列出最终影响。在本例中,严重程度评级将基于最终用户对刺耳响声的感受。
潜在失效后果可能发生在零部件层面,或在更高层次的装配上,也可能在完整的产品上,或在最终用户使用中或政府法规实施阶段[2],国际汽车工程师协会建议在组装、整个系统和客户视角的层面检查潜在失效后果[3],这可以通过列出组件在装配级别上的潜在失效后果、整个系统经历的潜在失效后果以及以客户感知失效的方式描述的最终影响来实现。这个最终的潜在失效后果是应该评估的严重程度。
如图2所示,“盖板松动”潜在失效模式可能包含三种相互关联的后果,这三种后果包括:
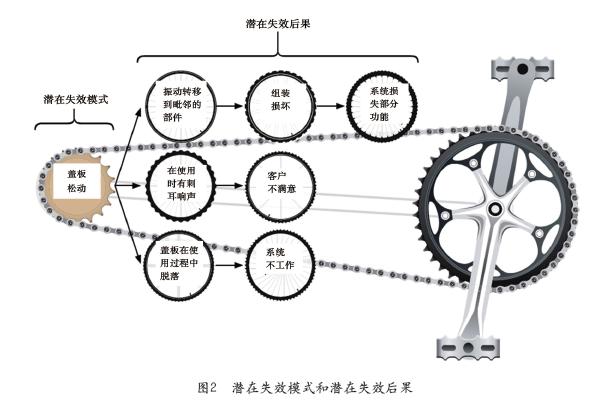
•振动可以传递到相邻部件。
•使用时可能会有刺耳响声。
•盖板在使用过程中可能脱落
在第一种情况下,潜在失效后果反过来在组装级别产生潜在失效后果,从而导致部分功能的丧失。在第二种刺耳响声的情况下,失效的影响停留在零件层面,最终的影响是客户的不满意。第三种失效模式,盖板脱落进而导致整个系统无法操作。
显示整个失效链似乎有些过多,但它可以使团队更清楚地解释DFMEA。例如,如果没有中间步骤,盖板脱落可能导致系统功能部分丢失或系统不可操作的原因可能不清楚。最终潜在失效后果的例子包括:
•噪声
•系统失效
•降低功能
•不能安装
•伤害最终用户
•火灾隐患
严重度是对失效后果的严重程度的估计,级别范围为1到10[4]。表格便于评估失效的严重程度。这有助于确保DFMEA之间的结果一致。有关DFMEA的表格可以在行业指南和各种书籍中找到。组织可以根据需要创建内部评估表。表1显示了严重度评估的通用表。

严重度应从最终用户的角度进行评估。例如,失效可能导致产品由于灾难性失效而完全无法运行。但是,如果该失效对最终用户是一个安全风险,那么严重性等级应该反映这一点。否则,在做出关于可能改进的决定时,可能不会认识到失效后果的严重程度。
潜在失效起因和发生频度
潜在失效起因是失败模式的根本原因[5],DFMEA应该假设零件是正确生产的,所以应该追究不正确的图纸规格造成的结果。
诸如“不适当”或“不充分”之类的模糊术语只应在无法得到更确切的描述时使用。“不适当”应该用于某些东西不够好的情况,例如当材料的性能不适合预期的用途时。“不充分”只能在某些物品的数量不够时使用,例如“材料的耐温性不足”。如果技术细细节描述不明确,系统DFMEA可能需要这些术语。
在为新概念做系统DFMEA或为客户特定用途实施DFMEA时,技术细节仍应尽可能描述得准确。在这里,对于有最终确定技术图纸的元件或组件,失效原因可能没有DFMEA中那么具体。如果系统DFMEA或应用程序DFMEA中的失效模式是由于缺少关键信息而发生的,那么缺少的信息可能是失效的原因。但是,潜在失效起因仍应尽可能具体,并应与技术图纸相关。
如果潜在失效模式零件断裂,是由于零件额定工作温度不适应客户的工作温度而导致的,则潜在失效起因可能是“材料性能不适合工作条件”。或者设计解决方案可以是一种潜在失效模式,例如当潜在失效模式“泄漏”是由“安装概念不适合操作条件”引起的。
潜在失效起因的例子包括:
•垫片厚度过宽。
•支架直径过小。
•底板表面粗糙度过高。
•销钉外径公差过宽,护板内径公差过低。
•套管材料耐温性不足。
•框架表面处理耐腐蚀性能不佳。
•铰链锥度角过低。
失效事件发生频度、检测度和现行控制
当前的预防控制是策划的确保失效原因不会发生的措施。一般来说,这些措施的执行是通过过程或规程来保证的。只有将要发生的行动才作为当前预防控制的一部分进行评估。测试通常用于检测度而不是预防,但如果在设计过程的早期进行测试,例如确定材料是否适合预期用途,则可以用于预防。预防措施包括:
•根据设计指南进行设计
•根据设计规则进行设计。
•使用结转设计。
•进行公差叠加计算。
•将设计与要求进行比较。
•使用额定温度符合要求范围的材料。
•从批准的材料列表中选择材料。
失效事件发生频度是指失效发生的可能性,级别范围定为1到10[6]。DFMEA中的失效事件发生是由于设计不当造成的失效,而不是生产或制造不当造成的失效。生产或制造过程的失效发生应在PFMEA中进行评估。
使用标准失效事件发生频度评价准则表来确保失效事件评估的一致性。如果标准或客户没有强制要求使用特定的表,组织应该创建自己的评估表。表2描述了一个失效事件发生频度评价准则表。
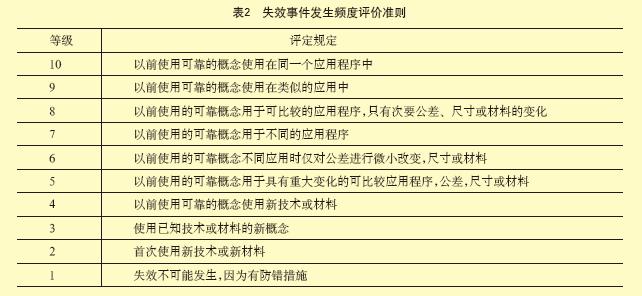
当前检测控制是用于评估设计的计划措施。由于采取了这些措施,因此不需要在DFMEA中进行特殊跟踪。通常,使用指定这些操作必须执行的过程或测试计划来确保这些操作的完成。表3列出了可能的检测度评价试验方法。
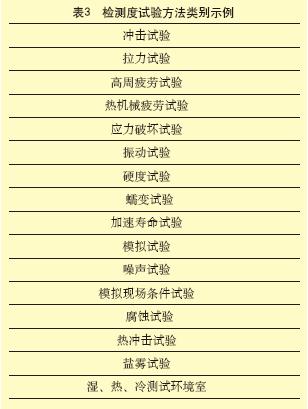
检测发现和解决问题可能性等级是检测发现失效原因或失效模式的能力,等级范围为1到10[7]。与失效事件发生率分级评价准则表类似。表4给出了一个通用的检测发现和解决问题可能性评级表。
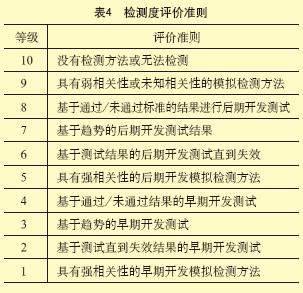
风险优先顺序数
严重度、失效发生频度和检测度相乘得到风险优先数(RPN)[8],风险优先数范围在1到1000之间。优先次序应该基于风险优先顺序数确定[9],在团队之间比较DFMEA评级是不合适的,即使是对可比较的产品也不合适,因为评级是凭经验主观的,每个团队的情况都是唯一的[10]。
风险优先数用于确定改进行动的优先顺序。理想情况下,有足够的时间和资源来改进所有风险优先数评级,但这种情况很少发生,因此应该使用两种类型优先级。首先,识别所有高严重度值乘以失效事件发生率值,这些将是最高级的风险,因为严重程度高加上发生率高意味着可能会发生严重后果。然后,再基于最高的总体风险优先数实施改进行动。
风险优先数不应该有底线分数。只要时间和资源可用,就可以继续实施基于优先级的改进,而不是试图将所有风险优先数提高到某个临界值以上。
改进措施和风险优先顺序数再评估
为降低风险优先数而采取的行动列在建议措施列中(参见图1)[11],这些措施适用于检测度或预防措施。严重程度只有在产品重新设计或预期用途改变时才能改变[12],针对失效事件发生和检测度的改进行动是尚未计划好的行动。因此,必须给每个人指定行动的责任和期限。执行该操作的人员可能不是DFMEA团队的成员,在这种情况下,应该指派DFMEA团队的成员负责通知执行操作的人员。DFMEA团队成员还负责确认实施并报告行动的结果。
采取改进行动,通过减少失效原因发生的机会来提高发生率评级,或者通过实现一个或多个新的行动来检测到失效原因或失效模式(如果发生失效)来改进检测度行动。再多的失效检测也不会降低失效严重度。因此,降低严重程度的唯一方法是重新设计,以确保潜在失效后果不会发生。当然,更改后的设计必须添加到DFMEA成果中并进行评估。
使用用于初始评估的相同评估表的评级改进操作,可能会导致与初始操作完全相同的发生率或检测度可能性评级,即使已经实施了更多的改进措施。
改变失效事件发生率可能比改变检测度更困难。例如,如果设计方案以前在不同的应用程序中使用过,并且已知是可靠的,那么执行额外的预防操作将不会改变发生率评级。在这种情况下,每执行一个动作,发生率就应该降低一个点。
检测度等级可以通过执行不同类型的测试方法来改变。例如,如果初始操作是基于通过/未通过标准的结果的测试,那么改进操作可以是基于趋势或直到失效的测试。
风险优先顺序数应在实施改进后重新评估。如果新的风险优先顺序数仍然很高,应考虑采取其他措施。如果某一DFMEA将被用作未来项目的模板,则应将已采取的改进措施及其评定级别移至当前控制部分,以确保其得到执行。
参考文献
[1]阿南德•皮莱和王进:“利用模拟推理改进的失效模式与影响分析”,可靠性工程与系统安全,2003年第79卷69-85页.
[2]D.H.斯塔马蒂斯:《六西格玛和超越:六西格玛设计》,圣露西出版社,2003年.
[3]美国汽车工程师学会:“国际地面车辆标准:J1739”,2009.
[4]佛利斯特W.波瑞佛格尔III:“综合企业卓越,第三卷-改进项目执行:超越精益、六西格玛和平衡计分卡的管理和黑带指南”,楼间架空通道书评,2008年.
[5]迪阿递目•普雷斯:“失效模式和影响分析指南:汽车、航空航天和一般制造业”,2003年.
[6]康妮M.博若尔主编:《认证合格的质量工程师手册》,第三版,质量出版社,2009年.
[7]南希•R•塔格:《质量工具箱》,第二版,质量出版社,2005年.
[8]克里斯汀•约翰逊:“返璞归真最高标准:从事失效模式影响分析工作的乐趣”,《质量进展》,2016年1月,第32页.
[9]迈克尔L.乔治,大卫•罗兰兹,马克.普莱斯和约翰•马克思:《精益六西格玛袖珍工具书》,麦格劳希尔集团,2005.
[10]美国汽车工程师学会:“国际地面车辆标准:J1739”,见参考文献3.
[11]美国德纳•吉恩,芭芭拉•思催拜尔和伊夫林•瓦尔纳:“六西格玛记忆慢跑者的设计”,GOAL/QPC,2004年.
[12]保罗•希伊,丹尼尔•纳瓦罗,罗伯特•西尔弗斯和维多利亚•凯斯:《黑带记忆慢跑者:六西格玛成功桌面指南》,GOAL/QPC,2002年.
作者简介
巴赛罗•马修(MatthewBarsalou)在德国汽车行业工作。他在德国达姆施塔特的威廉毕希纳设计学院获得工商管理和工程硕士学位,并在肯萨斯州海斯堡州立大学获得文科硕士学位。他是国际质量学会会员,美国质量协会会员,并担任美国质量协会统计学2021年主席。他是经过美国质量协会认证的六西格玛黑带、质量/组织卓越经理、质量技师和质量工程师。
编辑:Harris
失效模式和影响分析(FMEA)的重点大多在过程FMEA上,但需要设计FMEA(DFMEA)来确保识别和预防潜在的与设计相关的失效。作者提供了执行成功的DFMEA所需的行动的简明回顾,以帮助读者理解这种分析的过程和目标。